Precision Issues: Trusted Pipeline Welding Inspection Services for Crucial Projects
Wiki Article
Comprehensive Overview of Pipeline Welding Examination Treatments
Pipeline welding inspection procedures play a vital role in assuring that bonded links fulfill strict market criteria and specifications. From thorough pre-welding evaluations to detailed post-weld evaluations, a distinct examination procedure is crucial for keeping the structural soundness of pipes.Pre-welding Assessment Preparations
Before starting the welding process, comprehensive pre-welding inspection prep work are vital to guarantee the integrity and top quality of the weld joint. These preparations entail a careful evaluation of the materials to be welded, the welding tools, and the job setting. The products need to be examined for any kind of flaws, pollutants, or variances that might jeopardize the weld. This consists of monitoring for proper product grades, measurements, and surface problems. Pipeline Welding Inspection. Furthermore, the welding equipment requires to be inspected to confirm that it is in excellent functioning problem, adjusted appropriately, and suitable for the particular welding process. Any issues with the devices should be attended to without delay to stop defects in the weld. The job atmosphere need to be evaluated for tidiness, appropriate ventilation, and security steps to make certain a helpful setup for the welding procedure. By performing comprehensive pre-welding assessment prep work, prospective problems can be determined and settled early on, leading to dependable and top notch weld joints.Welding Procedure Certification
Comprehensive pre-welding evaluation preparations lay the foundation for the critical process of Welding Treatment Certification, guaranteeing the integrity and top quality of the weld joint. Welding Treatment Certification (WPQ) is a crucial step in the welding procedure that involves screening and certifying welding treatments to ensure they fulfill certain requirements and needs. The WPQ procedure commonly includes welding procedure requirements advancement, welding treatment credentials testing, and paperwork of the results.Throughout welding treatment specification development, necessary information such as the welding process, welding products, joint design, and welding specifications are specified to develop an extensive procedure. Subsequently, welding treatment certification screening is conducted to verify the recommended procedure's integrity. This screening often includes welding examination coupons that go through numerous mechanical and non-destructive examinations to assess the weld's high quality and adherence to the defined criteria.
In-process Weld Evaluation
Throughout the welding process, in-process weld assessment plays a crucial role in making certain the quality and stability of the weld joint - Pipeline Welding Inspection. This kind of evaluation includes checking the welding specifications, assessing the weld grain development, and detecting any potential defects or suspensions as they take place. By performing in-process weld assessments, welding drivers can immediately resolve any kind of problems that might develop, thereby avoiding additional problems and ensuring that the last weld fulfills the required specificationsCommon techniques used for in-process weld evaluation consist of aesthetic inspection, liquid penetrant testing, magnetic particle testing, ultrasonic testing, and radiographic screening. Visual evaluation is usually the very first step while doing so, permitting assessors to aesthetically evaluate the weld for surface area irregularities such as cracks, porosity, or incomplete fusion. Much more advanced approaches like ultrasonic testing and radiographic screening provide in-depth insights into the interior structure of the weld, ensuring that there are no covert flaws that could compromise the weld joint's strength and stability. On the whole, in-process weld inspection is vital for keeping the quality and integrity of bonded pipelines.
Non-destructive Testing (NDT)
Non-destructive Testing (NDT) is an important technique utilized in pipe welding examination to analyze the stability of weld joints without triggering damage to the bonded framework. By using various NDT methods, examiners can assess the quality of welds and determine any kind of issues or gaps that might jeopardize the architectural sturdiness of the pipe. Common NDT methods made use of in pipeline welding inspection consist of Radiographic Screening (RT), Ultrasonic Testing (UT), Magnetic Bit Evaluating (MPT), Fluid Penetrant Screening (LPT), and Visual Screening (VT)RT involves using X-rays or gamma rays to create photos of the inner framework of the weld, permitting examiners to spot flaws such as porosity, cracks, or incomplete blend. UT utilizes high-frequency acoustic waves to discover imperfections underneath the surface of the weld, providing detailed info about the dimension and area of issues. MPT and LPT are used to recognize surface-breaking flaws by applying magnetic bits or penetrant fluids to the weld location. Additionally, VT entails visual examination of welds to recognize any kind of noticeable flaws.
Post-weld Evaluation and Paperwork
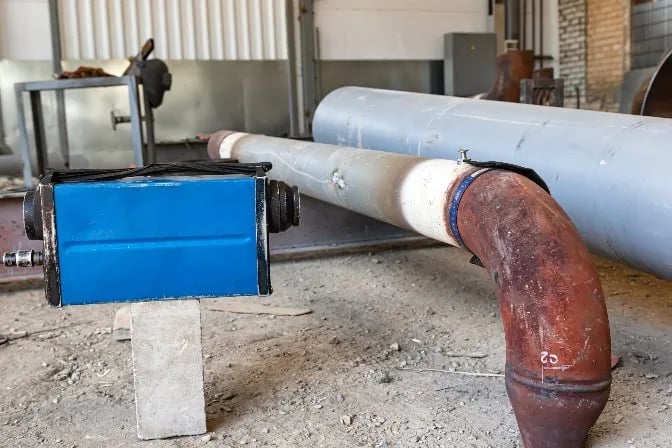

Paperwork of post-weld assessment findings is vital for preserving top quality control documents and ensuring compliance with sector criteria and policies. Comprehensive records ought to consist of information about the inspection techniques utilized, the place and nature of any type of issues located, and any restorative activities taken - Pipeline Welding Inspection. Appropriate documents not only acts as a record of the weld's quality but likewise aids in future maintenance and evaluation procedures
Final Thought
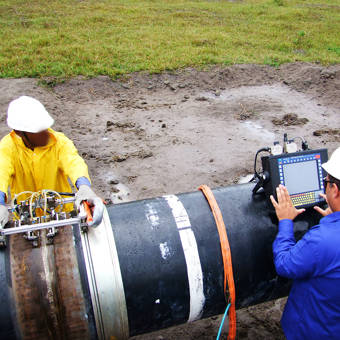
To conclude, pipeline welding examination treatments play an important function in making certain the high quality and stability of welds. From pre-welding examinations additional hints to post-weld paperwork, each action is vital in keeping the safety and effectiveness of pipes. By following well established treatments and conducting complete inspections, prospective issues can be identified and attended to prior to they lead to click to read more expensive repair services or failings. In general, adherence to appropriate examination methods is key to the success of pipeline welding jobs.
From thorough pre-welding examinations to comprehensive post-weld assessments, a distinct evaluation process is vital for preserving the structural stability of pipelines. By conducting in-process weld inspections, welding operators can promptly attend to any type of problems that may arise, thus avoiding further issues and guaranteeing that the final weld satisfies the called for specifications.
Common techniques used for in-process weld inspection include aesthetic assessment, liquid penetrant screening, magnetic particle testing, ultrasonic testing, and radiographic screening.Non-destructive Screening (NDT) is an important method utilized in pipe Get More Info welding examination to evaluate the stability of weld joints without triggering damages to the bonded structure. Post-weld inspection involves numerous approaches to examine the welds for problems, consisting of aesthetic assessment, color penetrant screening, magnetic fragment screening, ultrasonic screening, and radiographic screening.
Report this wiki page